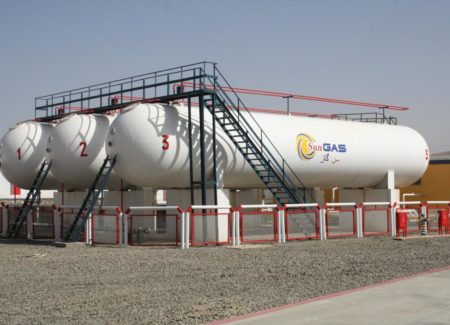
While flammability is the major safety concern with LP (Liquefied Petroleum) Gas it is not the only one. Good safety practice addresses the various hazards from production to consumption.
The term LP Gas embraces several products which while related have important physical differences which affect safety. If more than one type or grade of LP Gas is being handled, each should be clearly identified and segregated. All should be within specification, especially with respect to maximum permitted vapour pressure.
1. Large LP Gas installations should not be constructed close to large or sensitive populations. Populations should be restricted close to locations approved for large LP Gas installations. In planning or evaluating proposals for the location of LP Gas facilities, due account should be taken of the hazards created and of the risks associated with those hazards within and beyond the facility.
2. Space and separation distances are fundamental to safety at LP Gas facilities – large and small – and should be assessed for each location and observed.
3. Participants in the LP Gas industry should actively promote a safety culture within their own businesses and at industry level.
4. Personnel engaged in LP Gas operations should receive formal training by competent persons for their normal activities and for emergencies. LP Gas facilities should have emergency planning and response programmes appropriate to the hazards and risks which they represent. These include correct handling procedures to avoid injury.
5. Fuel grade LP Gas should be adequately odourised prior to entering the distribution chain. When LP Gas is required to be odour-free adequate alternative safety measures should be employed.
6. LP Gas cylinders and tanks should never be allowed to become liquid-full. Climatic conditions will influence the degree of fullage required but it is typical practice to fill to around 80% of the water capacity of the vessel. In some circumstances, overfill devices may be required to provide protection. In other cases cylinders and tanks should only be filled under the supervision of competent personnel
7. Above a certain quantity, LP Gas should be clearly identified during transportation, using classification numbers and appropriate warning signs.
8. Appliances and equipment for the handling, transportation and use of LP Gas should be fit-for-purpose, correctly installed and well-maintained. Sub-standard appliances, equipment and installations should be excluded if necessary by regulation.
9. Installers of appliances and equipment, and those responsible for service should be formally trained and should have reached a specified level of proficiency.
10. Cylinders for indoor use should preferably be filled with Butane or Butane-rich LP Gas mixtures although certain countries do permit the use of Propane cylinders indoors. Only those cylinders which are in use should be kept indoors. Whenever Butane and Propane are sold as separate products, cylinders should be readily distinguished and preferably fitted with different outlet valves so that they are not easily interchanged or used for natural gas appliances.
11. Consumer safety awareness campaigns are an essential part of LP Gas safety principles and they should emphasise:
- The quality/safety linkage for gas, appliances and equipment including safe practices
- The risks associated with inferior installation standards and/or practices
- The need for care and in particular for adequate ventilation
- How to recognise the smell of odourised LP Gas
- The action to take when gas is detected
Source: Except from “Guidelines for Good Safety Practices in the LP Gas Industry”- A Publication of World LP Gas Association