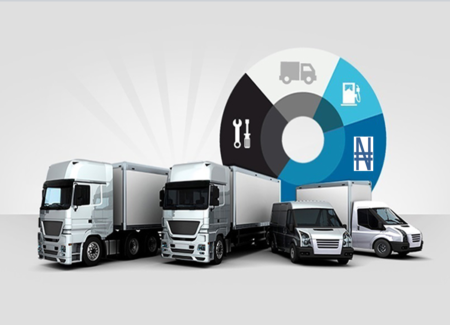
For years, under pressure from senior management, the fleet world has been scrambling to cut expenses. To their credit, fleet managers have responded to the challenge in a variety of ways, from “rightsizing” to extending the service life of their vehicles and making their fleets more fuel-efficient.
Another approach, however, has yet to be fully exploited by the fleet industry at large: reducing the costs associated with accidents. Now, with the advent of telematics and in-vehicle crash avoidance technology, fleets are hoping to reduce operating costs even further by preventing accidents. While promising, the full potential of these nascent technologies and their cost-benefit ratio has yet to be determined in practice.
Fortunately, though, there are proven traditional methods already in place that can achieve dramatic reductions in the cost of accidents if well implemented. Here, we’ll cover four:
- Reducing the cost of repairs,
- Reducing replacement vehicle expenses
- Increasing recoveries from third-party drivers, and
- Preventing accidents
REDUCING REPAIR COSTS
How is that possible? A few service providers focused on accident management have a full complement of licensed physical damage appraisers who scrub every repair shop estimate for savings on parts and labour. Experienced experts in collision repair, who have had successful careers as body shop technicians, estimators and managers or insurance industry appraisers, can assess how extensive damage may be, even in places not immediately visible in images of damaged vehicles. They are also adept at recommending the most cost-effective way to return these vehicles safely to the road.
For example, they can judge when parts can be repaired instead of replaced at a higher cost; when an OEM part must be used, or when a less-expensive certified after-market or used part can take its place.
They look for opportunities to complete two or more repairs with just one removal step, to save redundant labour charges, and to use less-expensive paintless dent repair rather than traditional methods. They also know when a repair that only affects the vehicle’s appearance can be postponed (as well as when damage that only appears to be cosmetic ought to be repaired).
CUTTING RENTAL EXPENSES
In the event of an accident, companies may resort to temporary replacement rental vehicles to prevent breach of contract with their counter-parties. The associated cost is often overlooked for savings potential. At roughly N50,000 a day, the difference between a 10-day repair cycle time and 12 days is N100,000, and between 10 and 20 days is N500,000; multiplied over hundreds of repairs, the excess expense easily reaches into the hundreds of thousands of Nairas. When those extra days are due to a complex repair or parts being in short supply, the cost is justified, but not when they’re the result of lapses that could have been avoided.
The key to keeping rental costs low is to keep cycle time – the time it takes for a shop to complete repairs – short. Shops should be held accountable to meeting agreed-upon repair schedules, which comes only with close monitoring. This best practice can be difficult to accomplish for fleets with limited human resources that have to patronise 3rd party asset management companies.
But it’s an asset/accident management service provider’s business to bring the necessary resources to bear on this effort.
However, monitoring and ensuring that the above is done can only work when the repair customer has leverage over the shop, and leverage is limited unless the shop receives meaningful volume from the fleet. Fleet accident management companies often have this leverage because, representing a large number of fleets, they’re able to provide volume repeat business that shops rely upon.
Fleets themselves sometimes contribute to unnecessarily longer cycle times when they delay authorizing repairs. Large fleets, where repair decisions are shared by a headquarters and local fleet manager, can run into this problem. In these cases, it’s important for all players to remember that every extra day it takes to authorize repairs is costly, and potentially by more than just one day of extra rental for each day of delay. Shops can be counted on to reserve a repair slot only so long before they put in another customer’s vehicle. In this case, it may be several more days before the fleet’s repairs can begin.
……To be Continued in Part Two!