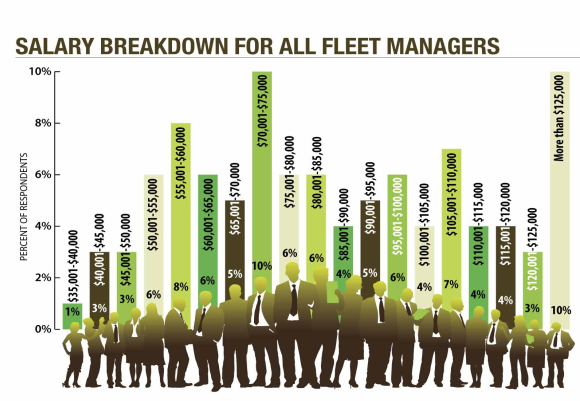
When looking at fleet managers salaries in 2014, pay levels increased compared to 2013, with 77 percent of the respondents to Automotive Fleet’s bi-annual Fleet Manager Salary Survey reporting a pay increase in the 2014 calendar-year.
Overall, 32 percent of fleet managers reported a salary of $100,000 or more per year. Also, of the 77 percent reporting a pay increase in 2014, 20 percent stated they received an increase of 4-6 percent.
LOOKING AT THE TRENDS
Looking at compensation by staff-managed fleets, managers with three to five additional staff members reported a median salary of $92,500; however, staff sizes appear to be shrinking, based on survey feedback.
“Our fleet staff decreased due to a change in corporate structure and philosophy, as well as cost containment and a change in focus. We had a complete reorganization of senior leadership, too, both globally and here in the U.S.,” said one fleet manager, who wished to remain anonymous.
Another fleet that is seeing a decrease in staff is Merck & Co, Inc. “Six years ago, there were 10 people involved in running fleet operations in the U.S., Canada, and Puerto Rico; now, it’s just me. This came as a result of mergers and consolidation, as well as putting much of the day-to-day fleet administration in the hands of our fleet management company,” said Scott Lauer, associate director, North American Fleet Administration, Merck & Co., Inc.
However, some fleets are seeing an increase in fleet staff: “We are taking on more responsibilities from the field, which justified adding a second person to manage these responsibilities,” said Shawn Dusosky, manager, fleet financial services at General Mills.
Fleet managers who have some post-graduate training or an MBA reported the highest median incomes, on par with previous survey results.
Additionally, fleet managers who oversee 1,000-plus vehicles reported the highest median salary at $102,500; however, like fleet staff, total vehicles are fluctuating right now as well.
“Our fleet size increased due to the acquisition of other companies, change in structure for field sales, and consolidation of subsidiary fleets,” said one fleet manager, who wished to remain anonymous.
And, while General Mills has seen an increase in its fleet staff, it is experiencing a decrease in its overall fleet size. “We just had an overall corporate downsizing, which resulted in the loss of 150 drivers,” Dusosky said.
Staff changes are also impacting fleets in another way: “One of the biggest changes I am seeing in fleet today is a larger dependence on FMCs for running fleets due to organizational downsizing,” said William Forsythe, certified automotive fleet manager (CAFM) for ADP.
DEALING WITH TIME CONSTRAINTS
Just about every fleet manager would agree: there are not enough hours in the day to get their jobs done. While 52 percent of fleet managers reported the ability to spend between 76 and 100 percent of their time on their jobs, only 47 percent of survey respondents noted that fleet was their only responsibility.
“Like many fleet managers, this is not my only responsibility. I also manage two separate profit & loss divisions. Dividing out time is always a challenge. I would suggest others lean more on their FMC and challenge them to provide the data that the fleet manager typically spends time providing,” said Dusosky of General Mills.
One of the biggest culprits responsible for taking up the most time every day? General communication, such as meetings and e-mails.
“One of my biggest challenges with time management is my calendar being filled up with meetings of very little value,” said Forsythe of ADP.
Lauer of Merck agreed that communication took up quite a bit of his time every day. “The deluge of e-mail that comes from everywhere (6,000 drivers, managers, HR, legal, operations, EH&S, etc.) is my biggest challenge with time management today. Some of it can be passed on to others, but many cannot. Trying to balance project work and daily responsibilities is also an issue, since my staff was reduced by two employees to just me last year,” he said.
Taking a different look at time management was Vicki Driessen, fleet manager at Faith Technologies, who noted that managing vehicle uptime was a continual challenge:
“As an electrical contractor, the biggest challenge in time management is the ‘unknown’ of when vehicles are needed. If we bid a job and are awarded the work, there are times a company vehicle — mainly a ½- or ¾-ton truck) is needed. Costs hinder me from retaining too many unassigned trucks at the corporate location,” she said.
WORKING WITH CHANGING JOBS
Each year, fleet managers also have a new set of challenges and changes to work with. In the past two years, some of the bigger changes include telematics, truck lightweighting, and vehicle selector options.
“The expansion of telematics and risk management is rising to the top of the list of the biggest changes I see in fleet today,” said Dusosky of General Mills. “Fleet is really a bunch of data, and telematics functionality is now allowing the micro-analysis of this data. How that data is captured, analyzed, and actioned is the hard question. Also, telematics functionality is an expensive proposition to sell to management. Risk mitigation is becoming an increasingly important issue, with the vast amount of technology that is being added to vehicles. Can we afford to not include these expensive options on vehicles, if they could prevent accidents?”
Driessen of Faith Technologies also sees a growing impact of technology on fleet today. “One of the biggest changes I see in fleet today is that trucks are being built lighter to gain better fuel economy. GPS technology has changed, meaning more trackability, which, in turn, means drivers are being held more accountable for their actions,” she said.
In addition to technology, the vehicles used in fleets are also changing.
“The biggest change for our fleet is reducing idle time and an increased emphasis on sustainability. We are ‘going green’ with different body materials, such as using aluminum and composites instead of standard steel. Also, we are working to make our trucks lighter for improved fuel economy,” said Bruce Ottogalli, transportation manager for United Water.
Source: Fleetfinancials.com