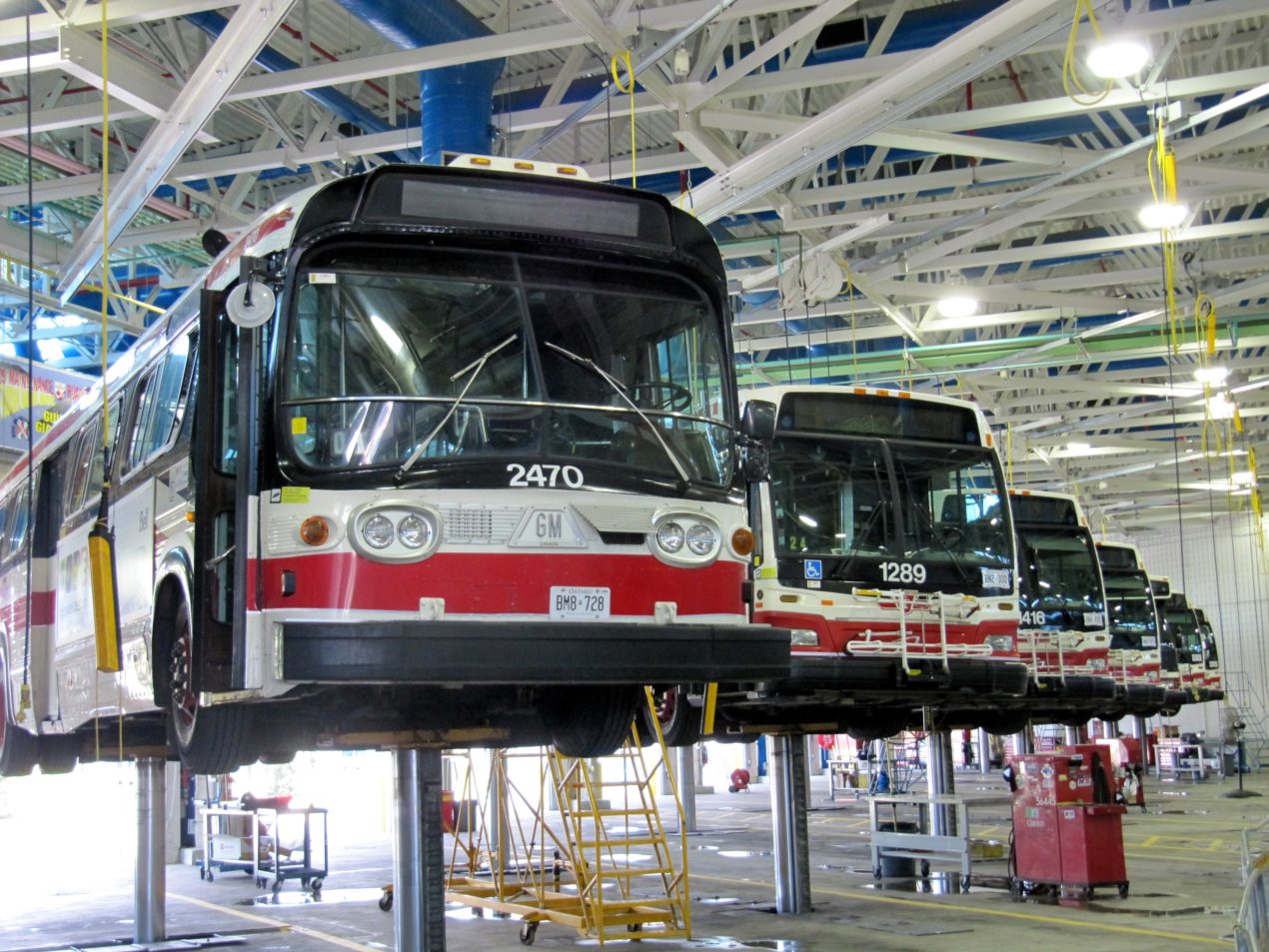
Fleet Maintenance Managers lead the activities of the maintenance department to ensure that fleet and heavy equipment is available, dependable and safe at all times. In some logistics companies, the job of fleet manager is a legacy position; having existed for years with a well-established job description. In others, the job may have mutated from what it may have been since the last fleet manager was hired. In some others however, it may well be a new opening being defined for the first time. They are often charged with overseeing maintenance preventative maintenance program and ensuring compliance with corporate policies and government regulations.
Most logistics firms usually prefer to hire fleet maintenance managers who have several years of experience as a fleet mechanic. Many also prefer fleet maintenance manager candidates who have excelled in leadership, organization, communication, inventory management and other managerial skills in past employment.
Some companies also prefer fleet maintenance managers that started their career as vehicle mechanics. Potential hires would also be expected to compliment this with a post-secondary training, which may include a certificate program or a degree in engineering or mechanics particularly when they are looking forward to working with large and well-structured organisations.
SKILL SETS REQUIREMENT
– The fleet maintenance manager will need to have knowledge on any Computerized Maintenance Management System (CMMS) in order to retrieve any information on vehicles, inventory, or employees electronically.
– They must have up-to-date knowledge of regulations emanating from the Industry or the regulatory authorities to make sure the company stays in compliance
– Readiness to remain available for emergency situations in an on-call status after regular work hours
– Experience with off-road heavy equipment is important
– Strong troubleshooting skills and excellent interpersonal skills and team orientation
– Sound oral/written communication skills in addition to analytical and computer literacy with particular experience using MS Office and fleet management systems
– Excellent time management and organizational skills with the ability to multi-task in a fast paced environment
POTENTIAL JOB DESCRIPTION
– Analyze maintenance costs and provide recommendations on fleet utilization and replacement
– Track fleet usage and maintain accurate inventory of equipment
– Assist in the development of maintenance budget by providing input relative to policy, costs and established metrics
– Carrying out all government and environmental statutory regulation on fleet to avoid infractions that may cause disturbance on daily sales and transfers
– Ensure the maintenance records (such as job cards, maintenance logs etc.) for fleet are accurate and up-to-date
– Negotiate service agreements to ensure cost efficiencies
– Complete performance reviews of maintenance staff and jointly determine areas of development and training requirements
– Communicate maintenance requirements to ensure maximum efficiency and implement correction actions as required
– Participate in the recruitment and selection of maintenance personnel and sometimes fleet drivers as required
– Identify maintenance employee training requirements and ensure successful completion
– Prepare regular weekly and monthly maintenance report and parts usage for management appraisal as required.
– Complete special projects and perform other duties as assigned.
– Lead plant personnel in day to day activities to ensure safe and efficient operations
– Coordinates staff regarding work methods, techniques and proper use and operation of equipment.
– Coach drivers on identification of faults and ways of reporting or providing continuous, constructive feedback regarding performance of assets in transit
– Investigates incidents and accidents, reports them to the appropriate Safety personnel and completes all required paperwork.
– Establishes schedules and methods for providing fleet maintenance and repair services in a timely and within-budget fashion
– Monitor fleet fuel consumption regularly, identify issues and rectify defects as required
– Implements fleet maintenance policies and procedures and ensuring compliance on corporate policies and SOP on fleet maintenance at plant level.
– Defines fleet maintenance work projects
– Forecasts additional funding needed for staffing, equipment, materials and supplies
– Coordinates outside fleet repairs, may identify and place orders for repair/replacement parts for vehicles and equipment
– Experience in managing and negotiating with Third Party Service Providers