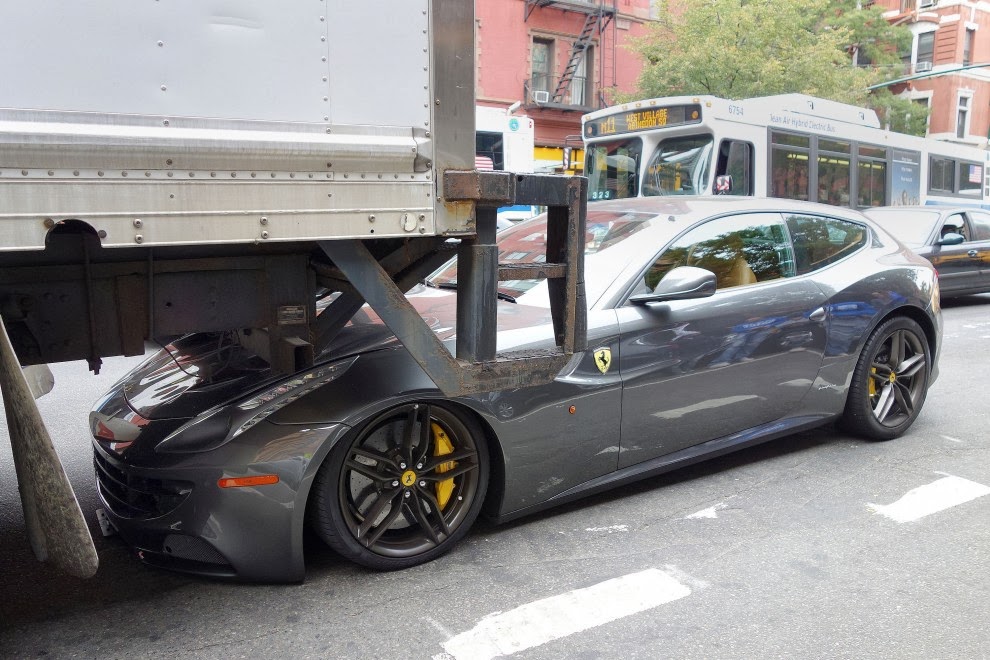
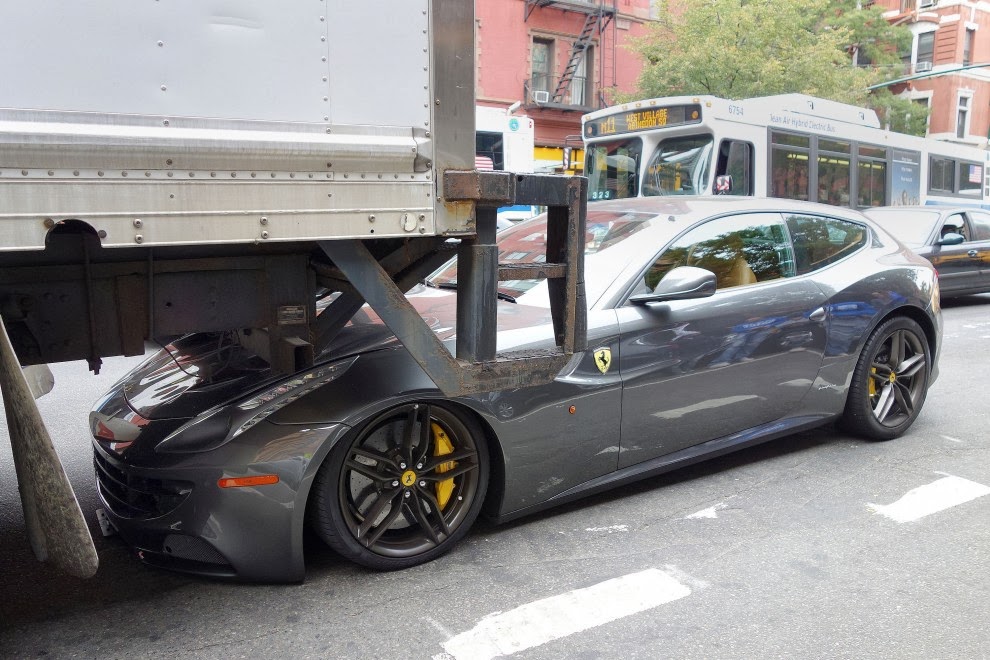
The Hidden Costs of “Small” Collisions
If they’re just scratches and dings, what’s the big deal? Fixed/stationary object collisions and backing collisions, while typically occurring at very low speed, can still be costly. The fact is the truck itself usually only sustains the scratches and dents due to the low speeds associated with these collisions. The same cannot be said for whatever got hit. After a collision, the scheduled deliveries and pickups will be delayed, impacting customer service. The need may arise to provide additional, uncompensated service to keep customers happy. Network efficiency will be affected as other resources are re-deployed to offset any potential operational impact. Over-time, additional fuel, mileage, additional risk, lost product all join the list to complicate a very bad situation.
Hard Costs of Collisions
The Heavy Duty Trucks carry an average load of about 30-40 Tons. Medium Trucks carry loads of between 15-25 tons. It varies of course, but most medium truck fleets maximize cube space before they even come close to 25 tons. That said; 15 tons of cargo is still a significant amount of mass when it hits an object. Since other vehicles are most often what is hit in parking lot collisions, it is important to note that other vehicles are expensive to repair.
A broken chrome grille of a Mack Granite could send a company back by as much as N300,000.00 and a badly damaged bumper by as much as N250,000.00. Add to this the cost of restoring body damage, other parts and paint.
Direct costs most commonly associated with these types of collisions include:
Cost to repair the vehicle or other object
Cost to repair the truck
Figuring out expenses to repair a car is reasonably straightforward, and adds up to a few hundred of thousand Nairas. But hitting a gas pump or knocking out an overhead bulk cement loader can be in the tens of thousands of dollars. There may also be incidental cost such as out-of-business compensation for affected truck owner!
Soft Costs of Collisions
Indirect or soft costs add up quickly as well, but can become more difficult to account for. It has been proven many times that soft costs can easily eclipse the hard costs by four times the amount. And what if the accident is serious enough to justify follow-up training or even termination of the driver involved? Driver training has a cost in lost time, and it can cost up to N250,000.00 (in selection, training and certification) to find and onboard a competent new driver (FACT 101: Although, not like many Nigerian Haulage Firms place a high premium on training). There could be possible injuries, medical bills and a lawsuit.
A collision that happened at less than 5Kmph could rack up thousands upon thousands of dollars in soft costs.
Measures to Avoid Parking Lot and Backing Crashes
The place of Focus
A decision to assist the drivers as much as possible in dealing with pressure is a good business decision. It pays to constantly remind drivers about focusing and finishing a task before moving onto the next one. As we heard one wise driver manager say once, “I ask you to do a lot, but I demand you do just one thing at a time.” For example, don’t start thinking about paperwork or the next loading slot until the truck is safely docked or parked. Focus is the keyword here.
Avoiding Fixed Objects
Pro-tread, a leading truck training organisation in the US recommends that the best approach to avoiding fixed and stationary object collisions is to:
Approach slowly
Scan the area you are approaching, including up
Get out and look: It’s not just for backing!
At these low speeds, it is easy to stop, activate the truck’s flashers, and hop out for a quick visual scan before making a tight maneuver or pulling under an awning.
Use Your Facilities More and Avoid Busy Lots Altogether
Depending on the size, duration and value of the haulage contract you have with your client, it may be very expedient for a 3PL logistics firm to site its own trailer park close enough to the distribution center of the client. In this manner, it becomes much easier to move into the distribution center at the prompting of your client rather than joining the mad rush within the yard by other companies seeking to secure a vantage space for their trucks. Another idea is simply to ban the truck from unusually busy or congested areas. For example, if you can keep your trucks out of busy fueling stations and tight parking lots, you’ll avoid a lot of incidents. When you know an area will be busy during a time frame, work with the store manager to avoid your delivery windows during that time.
Parking Lot & Backing Collision Avoidance Training
Training is still the most effective solution for the avoidance of backing collisions. The best option is to teach your drivers techniques for avoiding the need to back at all. This may require scouting a delivery area or talking to the manager of the facility beforehand. Of course, depending on your cargo or the type of facility, this is not always possible. When backing is necessary, drivers must be aware of their surroundings and know what is behind them. They must always remember the ‘Get Out and Look’ (GOAL) rule of backing or negotiating a dangerous turn. Remind them that the company expects them to re-inspect their surroundings as often as needed. It is a good practice to “get out and look” several times on a long back or in a very tight lot.
Moreover, drivers should be reminded that If they’re rushed, they’ll finish faster if they get it right the first time. Nothing slows a driver down more than hitting a pole.
Backing using a Motor-boy
Every haulage truck usually does require the services of both the driver and motor-boy. Although this still does not preclude the possibility of a backing accident happening. However, with good backing training for the driver and motor-boy, the collisions should be substantially reduced. You should require the driver and helper teams to properly demonstrate backing as part of a safety meeting. Ask your experienced teams of drivers and motor-boys for ideas about “narrow escapes” and “wild experiences.”
Additionally, this practice needs to be supported by a strong and actionable policy that holds both the driver and motor-boy accountable for a backing collision. If the truck is backing, the helper or team driver needs to be out of the truck and spotting the driver as he backs. Additionally, it’s never a bad idea for the driver to also “Get Out And Look.”
Backing Technology for Trucks
Back-up cameras in particular have shown success in reducing backing accidents. But like with any new tool, training with the devices is absolutely essential. Even the best back-up cameras distort the image behind the vehicle to some degree. They should only be used in conjunction with good backing techniques. Backing sensors, usually installed in the rear bumper, have also emerged as a technology solution. Again, as with the back-up camera, it is no replacement for good backing techniques.
Incentivizing Safety
Beyond training, there are other policies and practices that can have a positive impact on reducing backing accidents as well. As a manager, you can reinforce safety in a positive way, and enforce rules in a negative way. Many fleets have safety bonuses for going a certain period without an incident, or for completing all vehicle inspection reports on time.
On the flip side, negative reinforcement — such as termination — can be used for things like a second backing accident or for failing to report a collision. The most effective way to manage your drivers is to use both the carrot and the stick. Using both positive and negative reinforcement keeps drivers both accountable and encouraged.