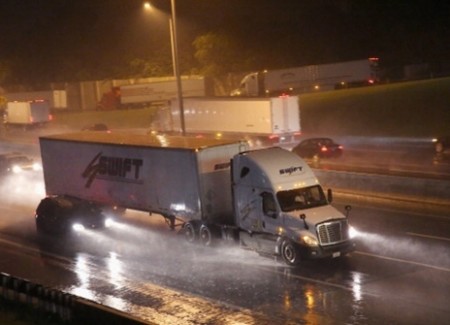
INTRODUCTION
Maintaining a safe and risk-free fleet operation is crucial to operating a successful business. Whether a truck fleet is small or large, minimizing driver risk and accident rates saves time, money, and even lives. Fleet operators should consider carefully the overall picture – not just insurance costs – when reviewing their financial ledgers.
A devastating truck crash for instance is not an isolated expense. The real cost, beyond truck and driver expenses, starts rising exponentially when damage to property, other vehicles, cargo, insurance premium hikes, medical bills and route delays are factored into the equation.
Calculating the real value of instituting fleet safety programs is a wise first step in maintaining productivity and profitability. Besides reducing the statistical probability of crashes, safety programs help boost the bottom line by preventing operational disruptions and promoting good morale in your workforce. Investing in a safety program also helps mitigate the less visible or obvious aspects of how fleets function. Indirect costs, including those involving lost production time and lowered morale typically are three times higher than direct costs.
Creating, implementing, and maintaining a thorough risk management and safety program is not only a must-do for fleets today, but is the only comprehensive way to control liability issues.
An in-depth fleet risk management and safety program considers the entire risk picture. Companies must first take into account regulations and the best practices derivable from those regulations.
Businesses must also examine how to effectively incorporate these best practices into their operation and company culture. They must look at all information and requirements and put it together to see how their fleet will really work. A business must make it as easy as possible so it is really effective and not so intrusive that your best practices are not functional. If it’s cumbersome and not manageable, it won’t work because those practices become only words on a paper.
WHOLISTIC FLEET SAFETY MANAGEMENT MUST INCLUDE:
- Regulatory compliance
- Risk management
- Loss prevention
- Human management
- Asset protection
- Employees
- Business
- Brand
THE KEY ELEMENTS OF A FLEET RISK MANAGEMENT PROGRAM
What are the key elements to a risk management program, and why are they so important in safe fleet operation?
WRITTEN POLICY: Avoid thick policy manuals with lots of cumbersome language. It’s just not effective. What is effective is task-driven policy.
PROGRAM ADMINISTRATION AND ACCOUNTABILITY: Everyone needs to be held accountable. Whether I’m working safely or being judged by accident rates, etc., it should be monitored and graded to make sure accountability is accomplished.
DRIVER SELECTION AND REVIEW: A driver selection and review policy should cover prevention of negligent entrustment, valid driver license (type & class) checks, assessment of acceptable driving records and a safety performance history check
DRIVER TRAINING AND DISCIPLINE: Extremely important step in the process, even for experienced drivers. Is the driver qualified and trained to be on the road? Initially, assess what driver training is required. Ensure training is reoccurring and includes refresher training on all safe driving topics. The goal of refresher training should be to keep drivers aware and refocused
DRUG AND ALCOHOL TESTING: Drug and alcohol testing policy should address the following areas: Pre-employment testing, Zero tolerance versus Second chance, Driver drug and alcohol training, Supervisor training and Record-keeping
ACCIDENT REPORTING AND ANALYSIS: For each incident, investigate the root cause and use that information to enhance the safety program. Every accident and near-miss should be investigated.
VEHICLE INSPECTION AND MAINTENANCE: Implement day-to-day maintenance and inspection. Additional areas of importance include accurate recordkeeping; pre- and post-trip inspections (conducted, documented, and reported); inspections by qualified personnel; and proper documentation of repair completion
RECORD-KEEPING: During statutory regulatory inspection, much of the time is spent looking at records. Having in place a systematic approach to how you can look at those records will make that process go more smoothly.
In addition, bench-marking is critical in reassessing a risk/safety policy. Keeping good records right from commencement helps to keep track of return on investment as the business progresses. Moreover, whenever progress report veers off the projection, good record helps in knowing where the deviation started and why things are turning out the way they are. Experts therefore advise that it pays to paint a picture of where your business sits today regarding risk/safety, as well as where you need to be each quarter.