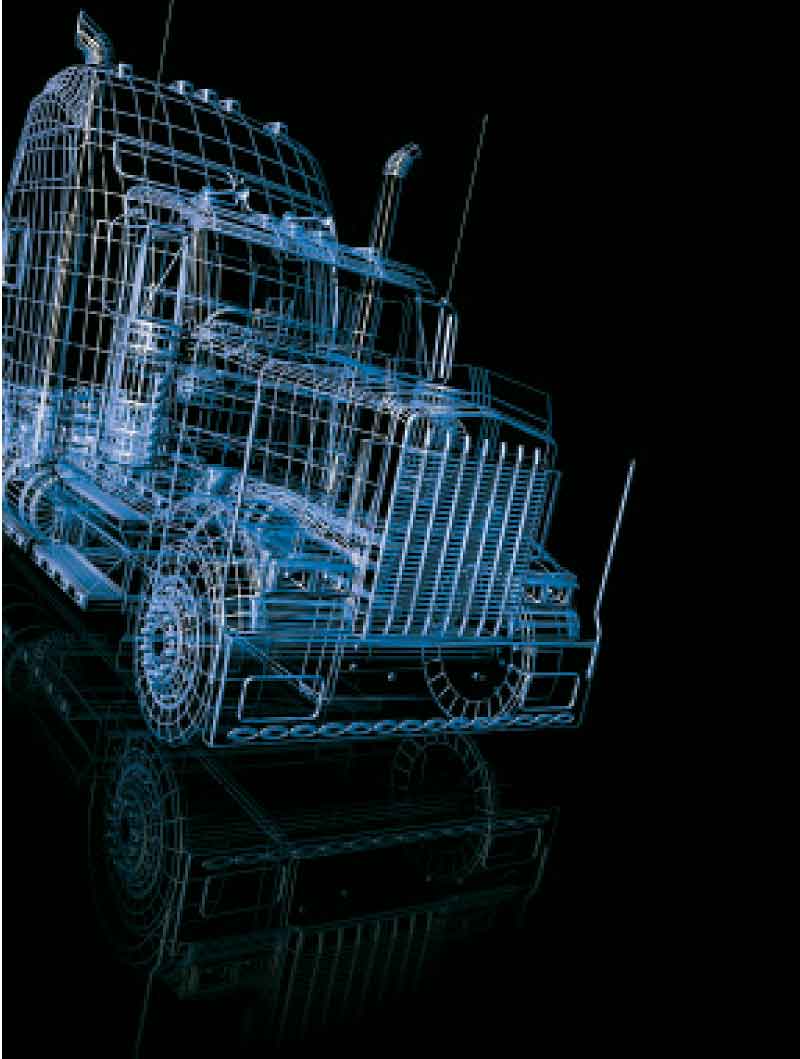
Generally speaking, Performance in any business is measured in terms of the relationship that exists between the resources deployed towards the sustenance of that business or enterprise and the end-result as measured by the output or value of product/service thereby generated.
Haulage business in Nigeria in the last 5years has witnessed tremendous growth in terms of the quantum of fresh capital injection that has gone into establishing new businesses or boosting the capacity of existing ones. As at today, investment in the haulage sub-service sector is estimated to be in the region of N500billion or more and boast of a steady annual growth rate of 10%. Findings from the CAC (Corporate Affairs Commission) indicate that about 5-8 haulage/logistics related businesses are incorporated weekly and the figure is nowhere abating! In fact, in a recent interview published by The Guardian Newspaper, a prominent haulage practitioner (The Guardian Newspaper of May 15th, 2011) declared that the sector is perhaps the next highest employer of labour after Manufacturing. Although, this may appear highly debatable, the declaration may not be too far from the truth.
It is also a known fact that the institutional framework established for the conduct of this huge contributor to our GDP Index is at best haphazard and at worst non-existent. (This is an area that will be treated in another discuss).
However, with the mindset that every investment in a profit-oriented business is undertaken with an eye on the returns on investment, it would therefore not be out of place to consider the factors that may assist the desire for improved performance through improved operational efficiency in the Haulage Industry. While the factors enumerated in this paper may not be altogether exhaustive, it perhaps may be a good starting point for any haulage business that is seeking to make an impact amongst the crowd.
This paper will address certain fundamental steps that can be taken (from an industry-player’s perspective) to improve performance in haulage operation. The analysis is broken into four key areas viz:
OPERATIONAL EFFICIENCY
FUEL MANAGEMENT EFFICIENCY
EFFICIENT EQUIPMENT AND SYSTEMS
EFFICIENT AND SKILLED PEOPLE
OPERATIONAL EFFICIENCY
Operational efficiency in haulage business is the capability of a company to deliver services to its clients in the most cost-effective manner possible while still ensuring the highest quality in delivery and service support. In order to attain operational efficiency, a company needs to minimize redundancy and waste while leveraging the resources that contribute most to its success and utilizing the best of its workforce, technology and business processes. The internal cost savings that result from operational efficiency enables the company to achieve higher returns on investment for its owner(s) or become more successful in the highly competitive zero-barrier haulage subsector. Some of the areas where a significant difference can be achieved in terms of operational efficiency are as follows:
Vehicle routing and utilization
Optimizing vehicle utilization
Fleet management solutions (Telematics)
Improving Cohesion through Sound Internal Communication
Vehicle Routing & Utilization
While many contract-based major industry players will have a vehicle routing template already predetermined by their clients comprising mostly large corporates within the Manufacturing Industry (and to which they are expected to align with strictly), many would probably have the liberty to define an optimal route assignment suitable for their operation. Now available in the market are various models of computerized vehicle route scheduling (CVRS) packages (that can be conveniently integrated into a robust Fleet Management Solution) which can collect and provide data to help measure performance levels and, in particular, show where certain routes or depots are more efficient than others in terms of, for example, vehicle fill, kilometers per drop and time utilization.
As an alternative (though not a best-fit), a simple deployment of the ‘Get Directions’ app in Google Map can assist in throwing up routing which can then be further fine-tuned through physical assessment to arrive at a fairly optimal vehicle routing plan. Whatever option that is chosen will definitely add value in terms of:
Reduction in journey times and vehicle mileage
Improvement in the variety of delivery schedules
Planning the most effective route
Maximization of the efficiency of deliveries
Reduction in the number of journeys and vehicles required
Optimizing Vehicle Utilization
In considering efficiency, nothing compares to getting MORE done with same or better still, LESS! A more optimal vehicle deployment is a sure way of not only cutting costs by making more efficient use of vehicles and drivers’ time, but also getting more returns per asset deployed. One way to do this is to prevent ‘Illegal Diversion’ of assets by unscrupulous drivers. Diversion may pose a clear and present danger to the lifespan of the asset and also lead to loss in revenue due to delays in reloading. An effective tracking system may be handy here. However, in view of the imperfect nature of the country’s telecommunication infrastructure, there may be need to compliment this with physical route surveillance.
Another method through which vehicle utilization can be boosted is ‘Return Loading’ which defines the process through which the spare capacity on an empty truck on the return leg of a delivery is put to a profitable use. Several haulage operators (mostly small to medium sized companies regularly operate return-loading, while the nature of contractual obligations entered into by large players may make it outrightly impracticable and non-permissible (if not condemnable) for them. However, leveraging on how return-loading otherwise called Back-loading is practiced in the more advanced world, it may be actually possible to redefine the contractual terms to give proper accommodation for what is called ‘Internal Back-loading’. This would mean allowing back-loading but strictly for the accommodation of other divisions of the counterparty’s business that are geographically dispersed. For example, a truck loading finished goods to a market/depot in the North may return with raw materials to the South where the factory is situated. In another instance, it may involve delivering to a client in the North and allowing for same truck to return with some portion for delivery to a West location (i.e. possibly a client to the counterparty’s major distributor) along the route back to the South (We will give a comprehensive assessment to this in a subsequent paper on this platform- Watch out!).
Fleet Management Solutions (Telematics)
Fleet Management Solutions, otherwise categorized under a field known as Telematics System, are applications that use computers to control and monitor remote devices or systems. Data collected through the management software in telematics systems can be turned into information that will help you to manage vehicles, drivers and operations more effectively. Some of these software come in ready-to-use solutions while some can be customized (depending on the budget or objective) and would most likely integrate pure reporting packages with mapping and text facilities or order- tracking systems which in turn are linked with ordering and accounting software. This may be set up as a single-user system or deployed via web for broader reach within the organization notwithstanding the geographical location. Ideally, such solutions should address problems associated with the following and should directly impact on overall efficiency:
Idling
Diversion
Harsh-braking
Over-speeding
Inventory management
Improving Cohesion through Sound Internal Communication
Most times, the actions or inactions of other units like Procurement, Inventory, Accounts or Warehouse unit can have a substantial impact on the operational efficiency of the fleet division. To this end, a sound work-place relationship and effective communication between fleet operations and other departments can’t be overstated. A deliberate and impartial measurement of performance for all officers across board will significantly assist in fostering and probably institutionalizing a culture of responsiveness and responsible internal relationship and commitment to the ideals of the business. Specific measurements that might affect haulage fleet efficiency can be used. Among these might be parameters that measure the number of late or failed deliveries associated with late procurement (Procurement Division) or errors in scheduling of vehicles for servicing (Maintenance Unit) as well as stock-outs or empty imprest (Accounts).
I do agree with all the concepts you have introduced on your post. They are really convincing and will certainly work. Still, the posts are very short for starters. May you please lengthen them a little from subsequent time? Thank you for the post.
@Polo Ralf Lauren; Thank you for your interest in our blog. We are also glad to learn that you are in agreement with the concepts we made reference to in our post. Regarding the length of the post, we will probably do some more research to up our game. However, please note that you can always click on ‘READ MORE’ to progress to the other pages of each post. We also will want to encourage you to sign up for regular notification of new posts. Thank you.
I pray one day the industry and entire haulage practitioners will acknowledge this great effort of your and reward you accordingly.weldon sir.
@Wale Megaloads; Thanks so much for the encouragement and prayers. Together, we shall work to uplift this industry. We appreciate you.